Before you try to fight warpage and other moisture-related issues, it’s important to understand what’s causing it and why.
When substrates are laminated and die-cut, a variety of problems can occur. For example, differences in moisture content between the printed topsheet and corrugated substrate can lead to warp in the finished product. Also, variations in moisture, combined with misapplication of the wrong adhesive, can create bubbles, “tunneling,” and score crack between the printed topsheet and corrugated substrate.
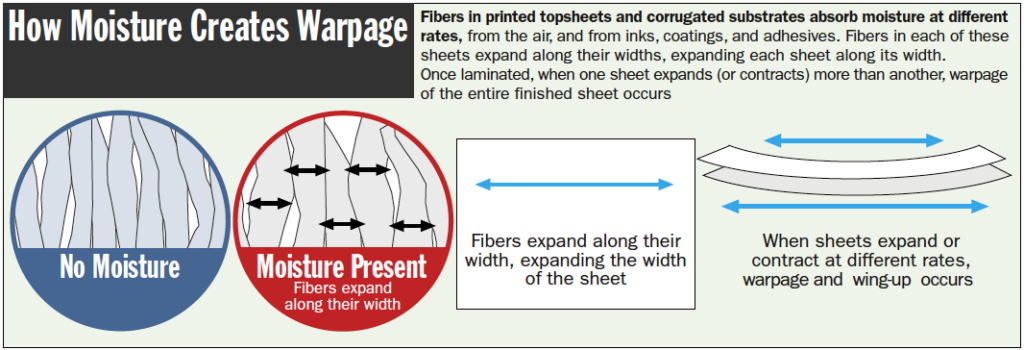
At a microscopic level, the printed litho sheet and corrugated substrates contain fibers that run in an opposite direction to the grain of the paper. From job to job, fibers in the cross direction react differently to conditions of added moisture or humidity, whether from the ambient air or by direct contact from inks, varnishes, adhesives, or other coatings.
When exposed to moisture, paper fibers swell and grow. Paper fibers in printed litho stock may expand at a different rate than those in the corrugated board to which they are laminated.
It is these different rates of expansion that cause warp in the finished sheet. Too much adhesive, or not checking moisture content prior to starting a job will many times create unnecessary waste and complicate final die-cutting and finishing operations.
(Excerpted from “Fighting Warp,” a recent issue of Evans Adhesive Solution Advisor. Download entire issue here.)